Ultra-high-resolution inkjet printing of functional materials has enabled new, additive manufacturing processes for devices that have typically been made using subtractive techniques, such as flexible electronics and optics. This method provides a more sustainable and potentially scalable pathway for fabricating electronic devices. Traditional inkjet printing is limited by minimum feature sizes in the tens of micrometers, but ultra-high-resolution inkjet printing – including the electrohydrodynamic inkjet (EHD) printing capabilities available at the Washington Clean Energy Testbeds — can generate smaller features by applying an electric field from the print nozzle. EHD printing is a fully additive manufacturing process that consumes less energy and produces less waste than subtractive processes, without sacrificing performance.
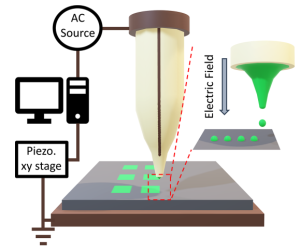
Why choose ultra-high-resolution inkjet printing?
Key advantages of ultra-high-resolution inkjet printing include sub-micron feature size capability, low-cost and high-throughput processes, and broad material compatibility.
Feature Size: Ultra-high-resolution inkjet printing can achieve patterning resolutions that significantly exceed those of conventional capabilities. For example, field-assisted EHD print heads are capable of forming droplets 1,000 times smaller than conventional inkjet printing, allowing for the deposition of features at and even below one micron in size. Inkjet printing down to the sub-micron regime exceeds the capabilities of large-area lithography used in processing thin-film silicon on glass for displays.

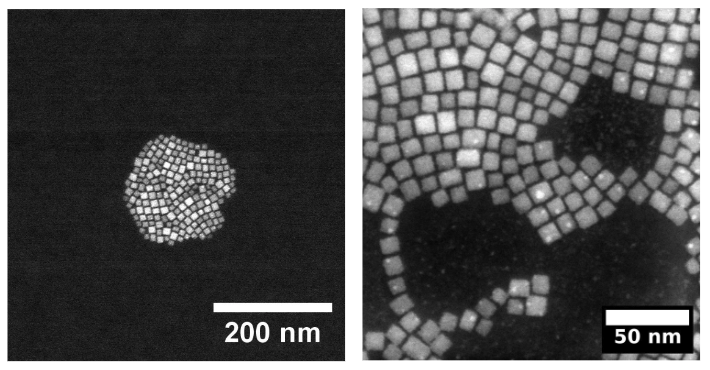
Low Cost and High Throughput: Traditional methods of achieving sub-micron feature sizes generally use a lithographic technique. While lithography can provide very high resolution and good reproducibility, it is a subtractive technology that produces substantial waste and is expensive to scale to a large area and high-volume manufacturing. The low cost and high throughput of ultra-high-resolution inkjet printing technology make it a promising alternative to conventional lithographic methods of manufacturing. Additionally, ultra-high-resolution inkjet printing can be used for economical prototyping before scaling to full manufacturing volumes.
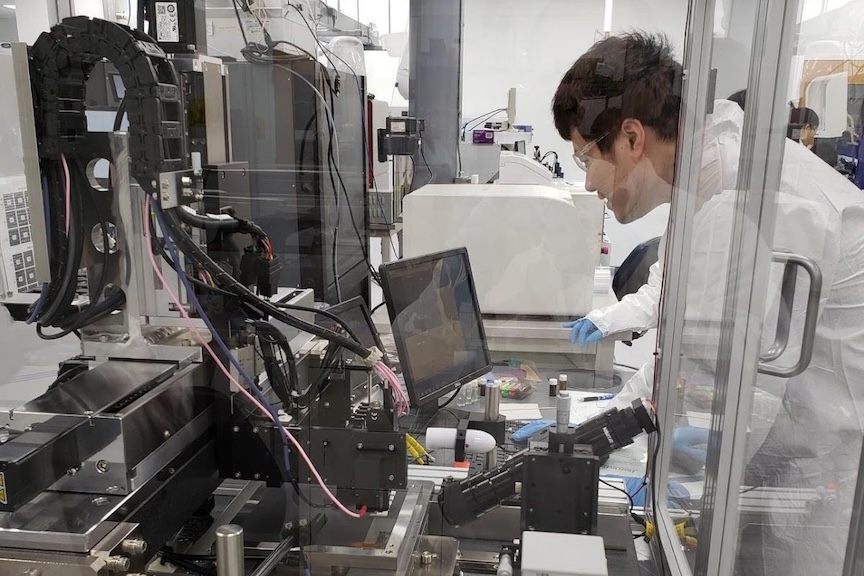
Compatible Materials: Ultra-high-resolution inkjet printing is compatible with a wide range of functional materials, including ceramics, semiconductors, and hybrid organic-inorganic materials. Possible applications include flexible electronics, sensors, energy storage devices, and metasurfaces.
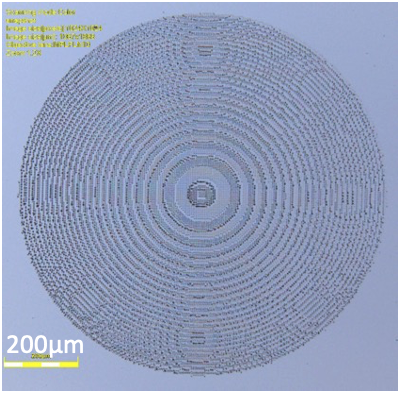
Expert Advice
To learn more about ultra-high-resolution inkjet printing, contact the Washington Clean Energy Testbeds at wcet@uw.edu. The Testbeds offer equipment and professional expertise on many different additive manufacturing methods and can help you find the optimal process for your specific needs.