Lithium-ion batteries have become the dominant battery technology in recent years due to several key advantages over other contemporary batteries, including high energy density for compact applications, rechargeability with minimal memory effect for longer battery life, and minimal self-discharge for long shelf-life. As a result, Li-ion batteries are preferred for countless applications such as consumer electronics, electric vehicles, and renewable energy storage. Manufacturing these batteries at scale requires efficient, reliable methods to keep up with high demand.
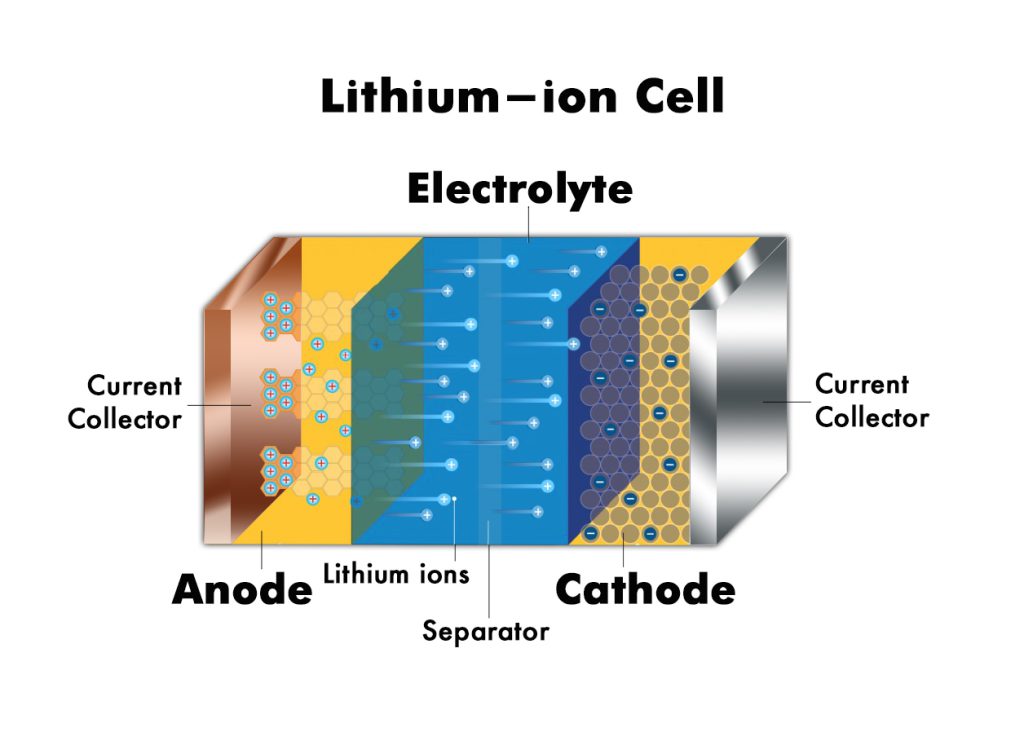
Roll-to-roll methods for battery manufacturing
Modern battery electrodes are typically fabricated via roll-to-roll methods for high-throughput manufacturing. Large rolls of anodes and cathodes can be prepared in a single, highly-automated coating step with techniques such as slot-die coating. Roll-to-roll systems are highly customizable and can be outfitted with a variety of coating and drying equipment to best meet the needs of a particular battery technology.
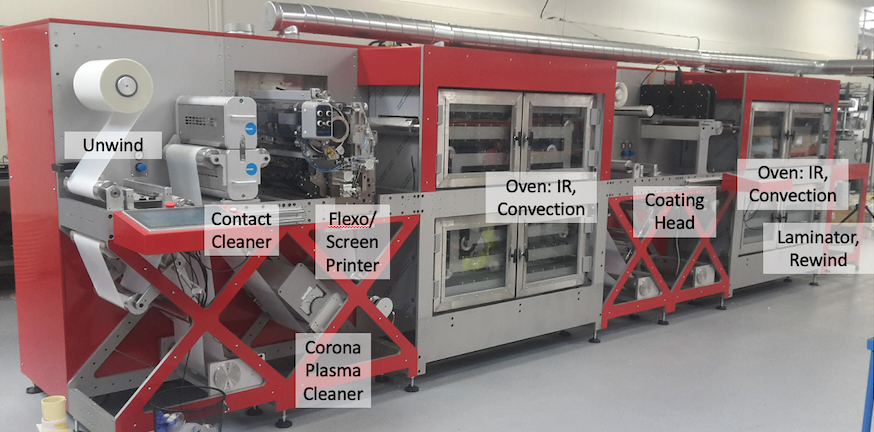
The roll-to-roll fabrication process for battery electrodes consists of several steps:
- Slurry formulation: The slurry is the liquid material that is deposited via a coating process onto a metal foil roll. For modern lithium-ion batteries, active materials are commonly lithium iron phosphate (LFP) or lithium nickel manganese cobalt oxide (NMC) for the cathode and carbon for the anode. In order to create a viscous slurry for deposition, the active materials are often mixed with high conductivity graphite and binders such as PVDF and/or carboxy methylcellulose. The specific viscosity requirements depend on the desired wet film thickness and coating method, and can vary significantly between different methods.
- Slurry deposition: The slurry can be deposited onto the substrate using coating methods such as slot-die, blade, comma/reverse comma, and more. In the example shown in Figure 3A below, an LFP-based cathode slurry was coated onto an aluminum foil via slot-die coating on a large-scale roll-to-roll system available at the Testbeds. A high pressure stainless steel syringe in conjunction with a syringe pump was used to deliver the slurry to the slot-die coater. The slot-die coating head used was specifically designed for use with high-viscosity fluids.
- Drying: After the slurry is deposited, it must be fully dried. In the example below, the slurry cast onto the aluminum substrate enters a convection oven, where it dries completely before exiting the oven and rewinding, which can be seen in Figure 3B. Once the desired coating length is achieved, the coated roll is placed back at the start to coat the opposite side of the foil. In some systems, a dual slot-die system is used to coat both sides simultaneously, reducing manufacturing time.
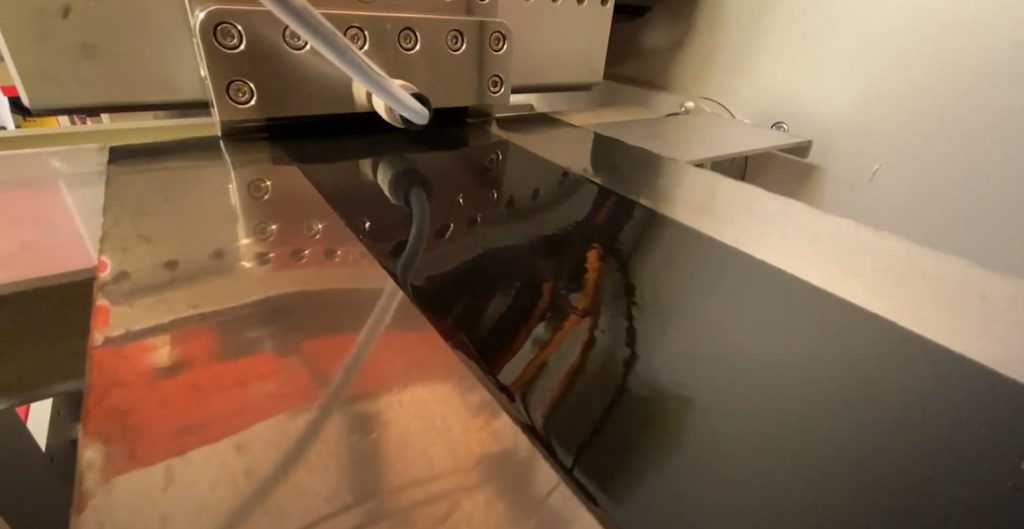
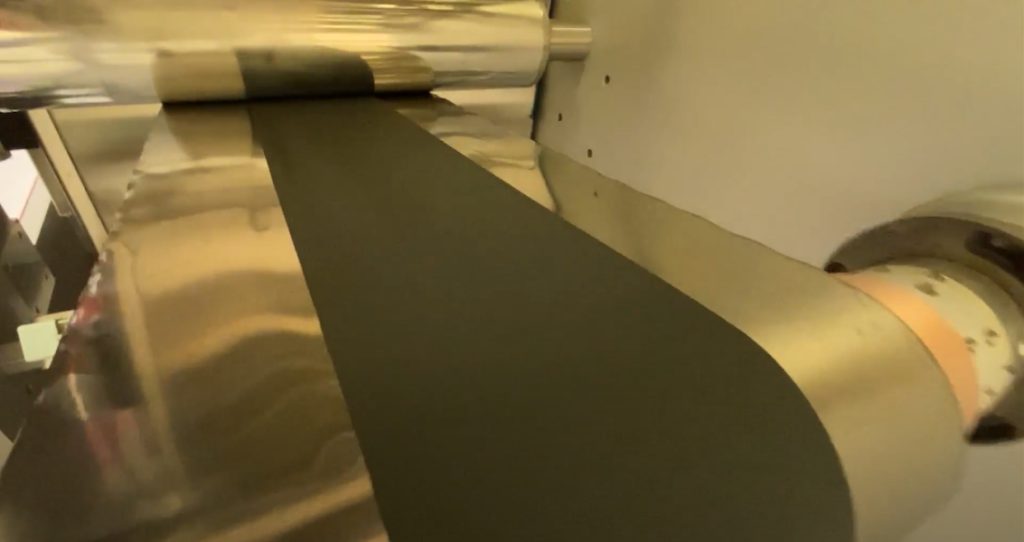
Expert Advice
To learn more about high-throughput manufacturing of battery components, contact the Washington Clean Energy Testbeds at wcet@uw.edu. The Testbeds offer equipment and professional expertise on many different additive manufacturing methods and can help you find the optimal process for your specific needs.