Screen printing, also known as silk screening, is not just a method for creating vibrant designs on fabric, but a pivotal technology in advanced manufacturing. This printing technique uses a mesh screen to precisely deposit inks on diverse substrates, which is ideal for applications that require detailed, durable patterns such as wearable electronics and flexible screens. Industries ranging from fashion to high-tech use screen printing for both small-scale and mass production because of its adaptability and precision.
How does screen printing work?
Screen printing involves transferring ink onto a substrate through a mesh screen, except where a blocking stencil inhibits ink passage. A blade or squeegee spreads the ink, filling the mesh apertures. During a reverse stroke, the squeegee presses the ink through these openings, allowing the screen to momentarily contact the substrate. This process deposits the ink, creating intricate designs and patterns. Traditionally using silk, modern screen printing has evolved to incorporate materials like nylon and stainless steel for improved durability and performance.
Components of screen printing
The basic components involved in screen printing include:
A) Ink: The medium used to create the image on the substrate.
B) Squeegee: A tool used to spread ink evenly across the screen.
C) Image: The design to be transferred.
D) Photo-emulsion: A light-sensitive chemical used to create the stencil.
E) Screen: A mesh stretched over a frame that holds the stencil.
F) Printed image: The final output of the screen-printing process.
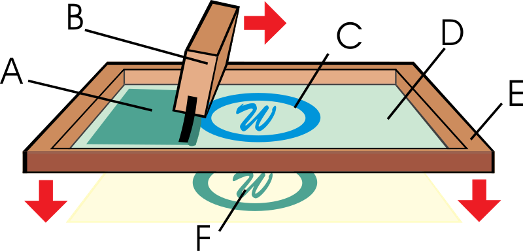
Screen printing for clean energy
Screen printing has been applied in the manufacturing of innovative clean energy technologies. One example is photovoltaic (PV) panels. The technique is used to apply fine lines of silver paste on the front of the panels to form the conductive contacts needed to collect and carry electrical current. The back of a solar panel is coated with aluminum paste to enhance conductivity and reflect light back through the silicon wafer, increasing the efficiency of the PV cell. This technique is now being applied to the manufacturing of printed, thin-film PV modules.
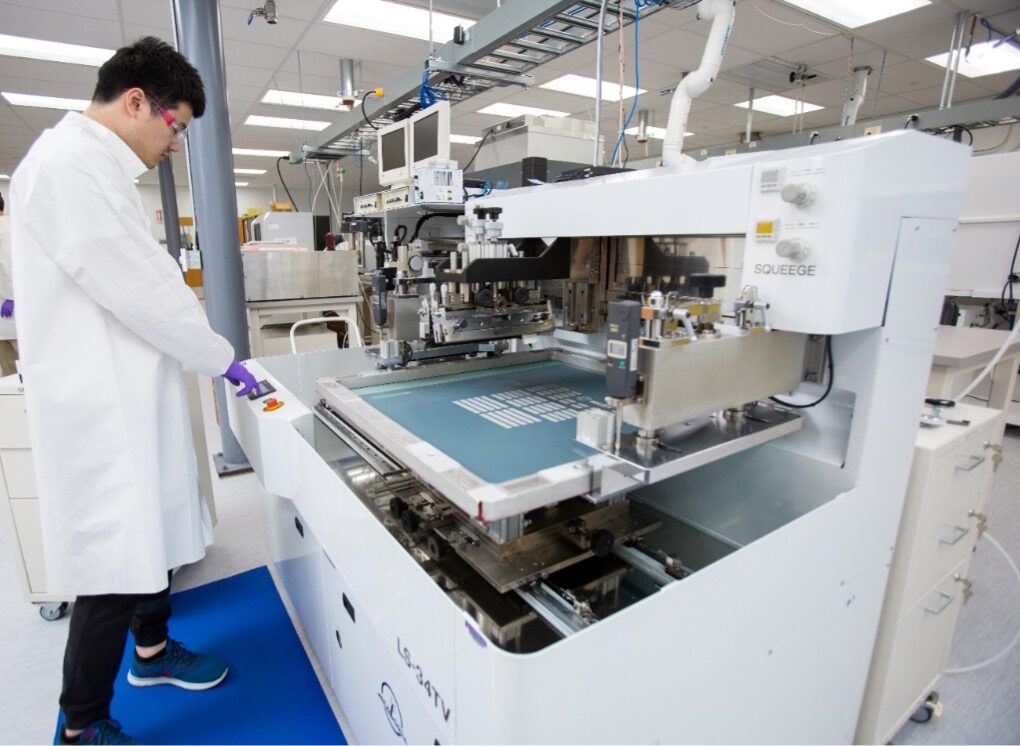
Screen printing for next-generation technologies
As materials technology advances, screen printing has found innovative applications such as creating circuits on flexible substrates for electronics that can be flexible, stretchable, and wearable; fabricating thin-film solar cells, electrochemical sensors, temperature and pressure sensors; and developing new display technologies. The ability to precisely apply thick layers of materials makes screen printing essential for fabricating advanced electronic and optical devices.
Key manufacturing advantages of screen printing include:
- Scalability: screen printing integrates smoothly into roll-to-roll manufacturing, boosting efficiency and production continuity for mass production.
- Reproducibility: screen printing offers consistent, high-quality outputs that are essential for industries that require uniformity across large volumes.
- Material versatility: screen printing is compatible with a wide range of inks and substrates, serving various sectors from textiles to electronics, including printing biosensors and smart clothing.
- Availability of inks: An extensive range of commercial inks for screen printing are available off the shelf, enabling rapid prototyping and customized production needs.
These advantages grant screen printing a significant role in modern manufacturing, and they point to a high degree of adaptability to the demands of future technologies.
Expert advice
To learn more about screen printing technologies, contact the Washington Clean Energy Testbeds at wcet@uw.edu. The Testbeds offer equipment and expertise on screen printing and can help you create your product safely, quickly, and with the best quality.