3D printing: an essential additive manufacturing technique
Modern three-dimensional (3D) printing began in the 1980s with the development of systems that used UV light to polymerize resins. This innovation paved the way for the introduction of stereolithography printing. Since the commercialization of the first 3D printers, the technology has seen widespread adoption across various sectors, demonstrating its versatility and capacity for innovation. Industries such as aerospace, automotive, healthcare, and construction actively utilize both desktop and industrial-scale 3D printers to solve complex problems and improve manufacturing efficiency.
State-of-the-art 3D printing at the Testbeds
The most advanced 3D printing system at the Testbeds is the nScrypt 3Dn-300, renowned for its innovative nanoFluid Dispensing (nFD) system. This 3D printer allows for the precise deposition of a wide range of materials, from conductive inks to biological substances to various polymers, at the nano to microscale.
The nScrypt 3Dn-300 is particularly distinguished by its surface scanning laser, which allows users to print 3D structures onto non-flat surfaces. Earlier generations of 3D printers deposit materials in 2D layers, which requires a planar surface and restricts the geometry of the printed structure. 3D printing that “conforms” to a design is crucial for creating highly detailed and complex structures that integrate different functionalities—such as electrical circuits—directly into printed outputs. Unlike standard 3D printers that are limited to a narrow range of plastics or resins, the nScrypt’s versatility extends to processing everything from low viscosity solutions and metal inks to solid polymers.
The nFD system’s ability to handle multiple material types in the same build process and its precision in material flow and placement set it apart from conventional 3D printing technologies. Moreover, the enhanced control provided by the nScrypt system minimizes material waste and boosts the efficiency of the manufacturing process.
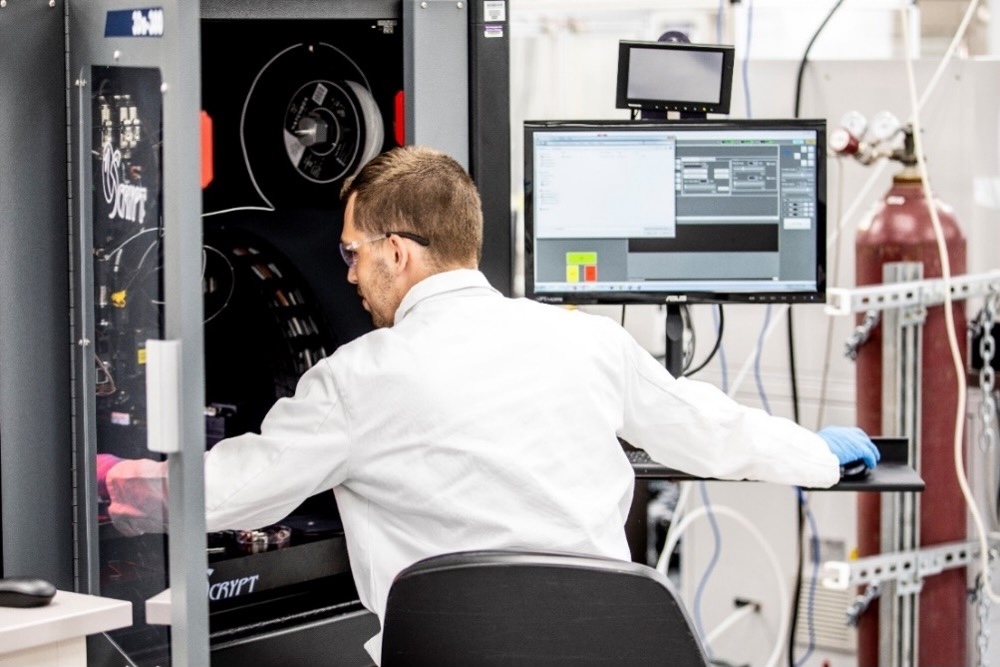
3D printing for clean energy and beyond
Advanced 3D printing technology has helped push the cutting edge of clean energy technologies, with one notable application being the development of new designs for energy devices. By utilizing the nScrypt printer to precisely deposit inks, researchers at the Testbeds have been able to test new materials for potential inclusion in solar cells to increase the photovoltaic efficiency of the panels. Another innovative project involves the development of temperature sensors for improved thermal management in battery and mechanical applications. Integrating these sensors directly into devices could greatly improve safety.
Conformal printing enables users to print active materials directly onto curved surfaces, allowing for advancements in various fields, such as electronics where the need for wiring can be reduced.
Flexible and stretchable electronics such as strain sensors have been made by printing silver nanowires into silicon substrates, and wearable strain sensors have been developed by printing liquid metals onto flexible substrates.

For designers and innovators in clean energy, advanced 3D printing offers several transformative advantages. The ability to prototype complex products quickly allows for rapid iteration and optimization cycles, which can drastically reduce the development time from concept to market. Conformal, multi-material printing also enables more creative and effective solutions, expanding the boundaries of clean energy technologies.
Expert Advice
To learn more about 3D printing technologies, contact the Washington Clean Energy Testbeds at wcet@uw.edu. The Testbeds offer equipment and expertise on 3D printing and can help you create your product safely, quickly, and with the best quality.